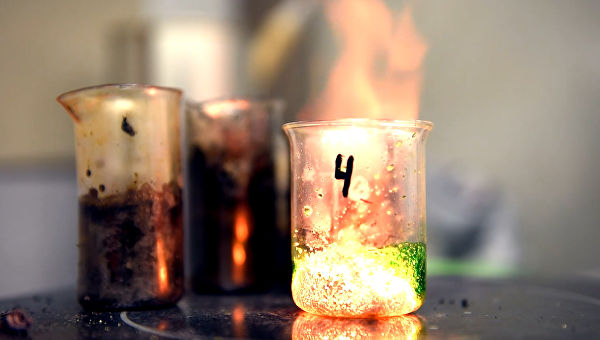
● Кроме традиционных способов формообразования, основанных на плавлении металла, последующем литье или деформировании слитков, в середине XIX в. возник принципиально новый способ изготовления деталей из порошков.
● Метод получения различных материалов и готовых изделий из металлических порошков путем их прессования и спекания называется порошковой металлургией.
● Однако прообразом порошковой металлургии можно считать кричный способ производства стали, при котором из-за недостаточности температуры в горне для расплавления больших объемов металла крупные изделия получали путем сваривания при ковке отдельных криц.
● Начало современной порошковой металлургии относится к 1826 г., когда русские инженеры П. Г. Соболевский и В. В. Любарский разработали технологию изготовления изделий и монет из порошка тугоплавкой платины путем прессования в холодном состоянии и спекания. «Русский способ» нашел широкое распространение в Европе, но, когда научились плавить тугоплавкие металлы, временно прекратил свое существование.
Все способы получения порошков условно можно разделить на две группы: механические и физико-химические.
● Эти способы характеризуются тем, что измельчение металла осуществляется без изменения химического состава, в результате воздействия внешних сил.
● Механические способы, в свою очередь, делятся на две группы: измельчение в твердом состоянии и получение порошков из расплава металла. Измельчение в твердом состоянии производится обычно в шаровых, вихревых, вибромельницах и мельницах планетарно-центробежного размола.
● В указанных мельницах, кроме вихревых, измельчение исходных материалов (стружка, опилки, грубые порошки) осуществляется путем дробления и истирания во вращающихся или вибрирующих барабанах между размалывающими телами (обычно стальные или твердосплавные шары).
● Следствием этого является загрязненность получаемых порошков продуктами истирания размалывающих тел и футеровки барабана. Отмеченного недостатка лишены вихревые мельницы, в которых измельчение исходных материалов происходит в рабочей камере в мощном вихревом потоке, создаваемом вращающимися в противоположные стороны пропеллерами. Размер частиц при шаровом размоле колеблется в пределах 40 ... 300 мкм; при вихревом — 50 ... 200 мкм; в вибромельницах и планетарно-центробежных мельницах получают порошки размером до 60 мкм.
● Общим недостатком способов измельчения в твердом состоянии является их низкая производительность Металлоподобные соединения разных металлов с углеродом (карбиды), кислородом (оксиды), азотом (нитриды), бором (бориды), кремнием (силициды), водородом (гидриды) обычно обладают высокой температурой плавления, а также высокими характеристиками твердости, упругости, химической стойкости, способностью к сверхпроводимости.
● Наибольшее значение для техники имеют соединения тугоплавких металлов (Ti, Zr, V, Nb, Ta, Mo, W) c перечисленными металлоидами. Для производства металоподобных тугоплавких соединений обычно применяют восстановительные процессы и прямой синтез из элементов, в том числе самораспространяющийся высоко-температурный синтез (СВС) и золь-гель процесс.
● Наиболее распространенным способом получения карбидов является науглероживание порошков оксидов металлов, или чистых металлов твердым углеродом. К порошку оксида металла или чистого металла добавляют углерод, обычно в виде сажи. Карбидизацию проводят в графито-трубчатых печах сопротивления в защитной газовой атмосфере (аргон, водород) или в вакууме.
В таблице 1 приведены свойства тугоплавких материалов.
Наименование металла
|
Символ
|
Номер
|
Атомная масса
|
Плотность, г/см3
|
Температура плавления, град
|
Титан
|
Ti
|
22
|
47,9
|
4,5
|
1665
|
Ванадий
|
V
|
23
|
50,94
|
6,11
|
1900
|
Хром
|
Cr
|
24
|
51,99
|
7,19
|
1903
|
Цирконий
|
Zr
|
40
|
91,22
|
6,45
|
1852
|
Ниобий
|
Nb
|
41
|
92,906
|
8,57
|
2470
|
Молибден
|
Mo
|
42
|
95,94
|
10,2
|
2620
|
Гафний
|
Hf
|
72
|
178,49
|
13,09
|
2222
|
Тантал
|
Ta
|
73
|
180,94
|
16,60
|
3014
|
Вольфрам
|
W
|
74
|
183,85
|
19,3
|
3410
|
Рений
|
Re
|
75
|
186,2
|
21,03
|
3180
|
● Наиболее распространен борокарбидный способ, при котором металл взаимодействует с карбидом бора.Если в качестве исходного компонента используется оксид металла, то боросодержащим компонентом служит только карбид бора.
● Процесс протекает по реакции 4МеО + В4С + 3С →4МеВ + 4СО в вакууме при 1500 – 1800oC.
● В случае исходного компонента является бескислородное соединение металла, то в шихту дополнительно добавляют борный ангидрид (В2О3) для удаления углерода, связанного с В4С. В этом случае, из-за высокой летучести борного ангидрида, процесс приходится проводить при атмосферном давлении в графито-трубчатых печах.
● Из-за высокой температуры процесса (1900 – 2000oC) происходитнеполное удаление углерода или даже науглероживание продукта до его содержания 0,5 – 2 %.
Наиболее хорошо разработан способ непосредственного азотирования металлов по реакции Ме + N → МеN. Температура азотирования 1100 – 1200oC, выдержка 1 – 2 ч.
● Необходимо применять меры по предотвращению окисления исходных металлических порошков с высоким сродством к кислороду. В частности, требуется тщательная очистка азота от кислорода.
● Основной способ получения гидридов – прямой синтез из элементов. К примеру, гидрид титана ТiH2 получают наводороживанием титановой губки при 900oC. После гидрировании полученный продукт подвергают измельчению.
● Гидриды циркония получают обработкой порошка циркония в водороде при 400 – 800oC.
● Наиболее распространен электроискровой (электроимпульсный) метод, при котором диспергирование металла происходит под действием электро- и гидро- или газодинамических сил, возникающих при взрывообразном протекании электрического разряда (10-40 кВ). Характерной его особенностью является значительная плотность выделяющейся в его канале энергии, высокая локальная температура среды при низкой интегральной температуре.
● Процесс электроэрозии сопровождается образованием ультрадисперсных частиц, конденсирующихся из паровой фазы металла, а также частиц, «отрывающихся» от разрушенных материалов. Изменением параметров разряда регулируют крупность образующихся частиц, получающихся из жидкой металлической фазы. Частицы, вылетающие с большой скоростью из зоны разряда, резко охлаждаются в межэлектродной среде, что важно для формирования их структурных свойств.
● Метод электроэрозии позволяет как разукрупнить порошки и гранулы, так и получать высокодисперсные порошки, а также композиционные материалы на их основе (например, системы М — С, М — О, М — N и др.). В последнем случае процесс ведут в активных средах, участвующих в реакциях с парами металлов.
● В промышленных установках электрические разряды осуществляются в зернистом слое частиц диспергируемого материала. Благодаря массовости разрядов а рабочем объеме аппарата эти установки могут иметь высокую производительность (десятки килограммов в час). При этом к форме диспергируемых частиц нет особых требований, что даёт возможность переработки металлоотходов — стружки, скрапа.

Рис.2 Электроэрозионная установка для получения порошков: 1 — электрод; 2 — металлические гранулы; 3 — жидкость; 4 — источник тока
|